Check Valves for Vacuum Systems
New and Improved Check Valves by ANVER – One Piece Casing for Leak Proof Construction
Competitively priced and used in virtually every vacuum application shown on our website

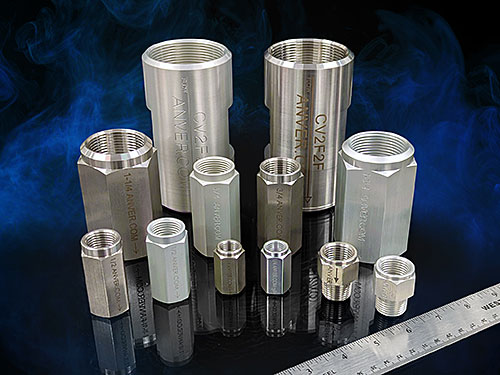
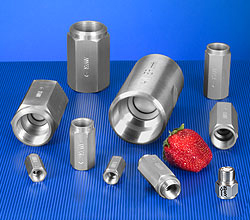

|
These high-quality Check Valves are specially manufactured in the U.S.A. by ANVER, for ANVER lifting systems. Versatile, one-way Check Valves work with nearly all of ANVER’s vacuum applications where vacuum loss prevention is required. ANVER Check Valves can operate in any position with the highest flow available making them the best overall value for mid-range vacuum level systems in the industry.
Features
- One-piece, airtight, leak-proof design for years of trouble free service.
- Sturdy, anodized aluminum body is compact and will not crack like other material.
- Optimum flow design for use with all vacuum applications and very large flow rates (Cv).
- Spring loaded to operate in any orientation.
- Low cracking pressure allows you to get the most performance from your pumps.
- Precision internal plastic valve with stainless steel springs eliminates corrosion from water contamination.
Specifications
- Maximum pressure: 230 psi
- Temperature: 0° to 200°F (-18° to 93°C)
- Internal seals: Nitrile Butadiene Rubber (NBR)
- Body: Anodized aluminum or stainless steel (SS)
- Internals: Acetal plastic
- Spring: Stainless steel
Tips
- For a 1-1/2″ check valve, use the 2″ check valve with adapters (GPR2X112) to allow for a maximized flow rate (Cv). The reduced restriction is worth the minimal added cost of adapters.
- The main restriction of a vacuum system is at the check valve. By using a smaller pump, the flow will increase at this point, thereby making it the most economical way to increase a vacuum system’s performance.
- Use a filter prior to the check valve to eliminate debris from clogging the valve.
- Stainless steel Check Valves are suitable for filtered water applications that contains no debris.
|
Note: These check valves were specifically designed and built for ANVER’s vacuum lifting systems, and have been proven in actual vacuum system installations. Ordinary check valves designed for compressed air systems are unsuitable for use in vacuum systems and can adversely affect your system.
*Cracking Pressure refers to the minimum pressure differential needed between the inlet and outlet of the valve to lift the plunger off its seat to generate flow.
**Flow Coefficient {Cv} is determined by the flow of water through a valve at 60°F in US gallon/minute at a pressure drop of 1 lb./in2. Cv is a relative value that allows comparison between different valves. The actual flow rate in SCFM is dependent on other variables within the application. Since water is a non-compressible liquid and air is a compressible gas, the inlet and outlet pressure are needed to determine actual flow of air since the density of air changes with pressure.
General equation for air flow when Cv is known is:
SCFM = (Cv x (∆P x ((Pin-∆P) + 14.7))1/2) ÷ 1.024
Where Pin = Inlet Pressure & ∆P = Pressure Differential
Flow rates shown are based on the formula for air flow to atmosphere calculated by:
SCFM = Cv x ((((PSIG+14.7) x 0.46) x ((PSIG+14.7)*0.54))1/2 ÷ 1.024
Where gauge pressure, PSIG, is assumed to be negligible.

13600241A